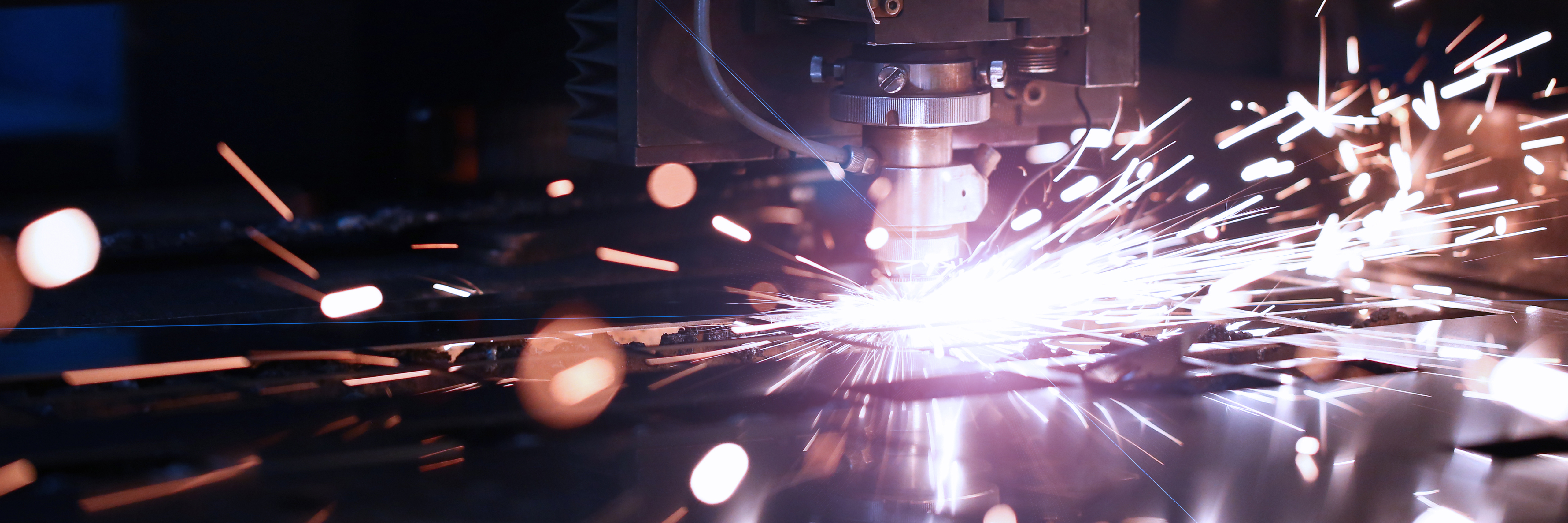
3-D scanning
CAD/CAM softwares to accurately machine the tooling.
Testing of non-dimensional attributes of samples for a better understanding of the materials involved and the functional parameters of the products.
11238 different Tools & Dies.
VMC Machines
CNC Wire Cutting Machines
CNC Milling Machine
Pantograph Machines
Drilling Machines
CNC Machining Centers
CNC Lathe Machines
Electronic Spark Erosion Machines (EDP)
Centerless, Cylindrical 6 Surface Grinders
Digitally Controlled, CNC and 3 Quadrant Measuring Machine
Robotic SPN For Critical Operations
Lathe Machines - Manual, Semi-Automatic, Turret
Boring Machines
Broaching Machines
Induction Hardening Furnaces
Shaping & Planning Machines
Milling Machines
Grinders - Centreless, Cylindrical, Surface
Welding Machines— MIG, ARC & SPOT
120+ mechanical and hydraulic sheet metal presses
Capacity to process upto 1000 tons of steel each month
Deep drawing execution capacity upto 200 mm in depth
Equipped with computerised shearing machines
Mechanical power presses ranging from 60 - 350T and Double action hydraulic power presses of 150 -300T
Automotive grade fasteners as per DIN, JIS, SAE and BS are welded as per defined automotive standards to stampings to achieve the required torque strength
Robotic welding machines for critical high accuracy sheet metal components
Supervised by qualified rubber technologists using fully integrated laboratory.
200 tons of tailor made rubber compounds processed each month as per customer and product requirement.
Tested to obtain desired pre-moulding, ageing, durability and physical curing characteristics, tensile strength, elongation, hardness, ageing and durability.
Correct grade polymers and chemicals are used to match intended use.
Scientifically inventoried mixes are kept in air conditioned, environment-controlled chambers.
The entire process is monitored batch wise.
Rubber produced is tested on equipments such as Rheometer, Mooney Viscometer, Dynamic & Static Testing Machines, Ultrasonic Testing and Hardness Testing equipments etc. to ensure meeting of customer and field requirements.
Largest infrastructure in Asia dedicated solely to aftermarket operations.
Producing nearly 800,000 general moulded rubber parts every month.
More than 115 sophisticated PLC controlled machines of German, Korean and Taiwanese origins for Injection Moulding, Compression & Transfer Moulding and Cold Runner technology.
Automated phosphating plant with programmable transporter.
Automatic degreasing machines.
Shot & sand blasting machines for pre-moulding and final finish to the metal surface.
Ability to do various finishes including E-Coating and PU Coating.
Control over the range of coat thickness, in microns, to meet different salt spray standards.
Strict Process Control mechanism is built in the machine to control the required quality of paint surface finish.